Centerless Grinding on Surface Grinders An Overview for Exporters
Centerless grinding is a precision machining process that has gained significant popularity in various manufacturing sectors. Unlike traditional grinding methods, centerless grinding does not require the workpiece to be mounted on centers or fixtures. Instead, it is supported by a regulating wheel and a grinding wheel, allowing for improved efficiency, accuracy, and reduced setup time. This article explores the unique aspects of centerless grinding on surface grinders and its implications for exporters in the global market.
The Centerless Grinding Process
Centerless grinding entails a straightforward yet effective method of grinding cylindrical parts. The process is typically carried out using two grinding wheels the grinding wheel, which does the cutting, and the regulating wheel, which controls the feed rate of the workpiece. This setup provides several advantages
1. Increased Production Rates The ability to continuously feed materials into the grinding area facilitates higher throughput, ideal for high-volume production runs. 2. Consistent Part Geometry By applying constant pressure and contact, the centerless grinding process ensures consistent diameters and surface finishes, which are critical in parts manufacturing.
3. Versatility Centerless grinding can accommodate various materials and sizes, making it suitable for industries ranging from automotive to aerospace.
Applications in Surface Grinding
While surface grinders are traditionally used for flat surfaces, the integration of centerless grinding on surface grinders enhances their capabilities. This is particularly advantageous for applications requiring intricate geometries or special surface finishes. For exporters, understanding the potential of centerless grinding on surface grinders can significantly broaden the product offerings in international markets.
Market Trends for Exporters
As global competition intensifies, exporters need to stay attuned to market trends that influence demand for precision machining processes, including centerless grinding
. Here are some noteworthy trendscenterless grinding on surface grinder exporters
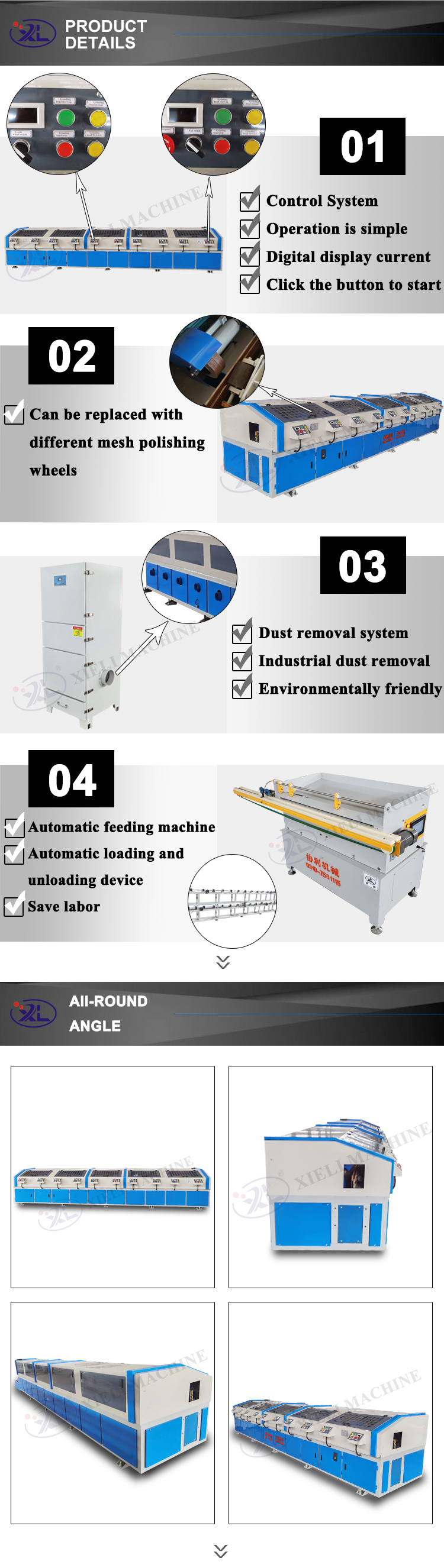
1. Rise in Automotive and Aerospace Sectors The demand for precision-engineered components in the automotive and aerospace industries fosters a favorable environment for exporters specializing in centerless grinding technologies.
2. Growth of Advanced Materials The increasing use of advanced materials such as composites and high-strength alloys necessitates advanced machining methods like centerless grinding to achieve desired specifications.
3. Focus on Automation The trend towards automation and smart manufacturing processes provides opportunities for exporters who can offer technologically advanced centerless grinding systems that integrate with Industry 4.0 solutions.
Challenges in Exporting
While the prospects of exporting centerless grinding technologies are promising, exporters must navigate several challenges
1. Regulatory Standards Different countries have varying standards and regulations governing manufacturing and quality control. Exporters must ensure compliance to avoid penalties and maintain a good market reputation.
2. Technological Adaptation Understanding the specific needs of international customers and adapting technology to meet those requirements can be a significant hurdle.
3. Competition The globalization of manufacturing means that exporters face competition from both local and international players. Establishing a unique value proposition through exceptional quality and customer service is vital.
Conclusion
As the landscape of manufacturing continues to evolve, centerless grinding on surface grinders represents a critical area for exporters. By leveraging the advantages of this technology, exporters can meet the growing demand for precision components across various industries. Understanding market trends, addressing challenges, and delivering innovative solutions will be key to succeeding in this competitive arena. With the right strategies in place, exporters can not only thrive but also contribute significantly to the advancements in machining technologies globally.