Understanding the Importance of Coolant in Centerless Grinding
Centerless grinding is a vital manufacturing process used to produce high-precision components. This method differs significantly from traditional grinding as it involves no spindle, enabling quicker and more efficient operations. Nevertheless, a crucial aspect often overlooked in centerless grinding is the role of coolant. The use of coolant not only enhances performance but also extends the life of the equipment and ensures optimal results.
Understanding the Importance of Coolant in Centerless Grinding
Moreover, coolant facilitates the removal of metal chips and particles that accumulate during the grinding process. These particles can cause unwanted marks or scratches on the workpiece surface if not properly washed away. The coolant acts as a cleaning agent, washing the debris away and ensuring a smoother, higher-quality finish. This is particularly important in industries that require strict adherence to specifications and tolerances.
famous centerless grinder coolant
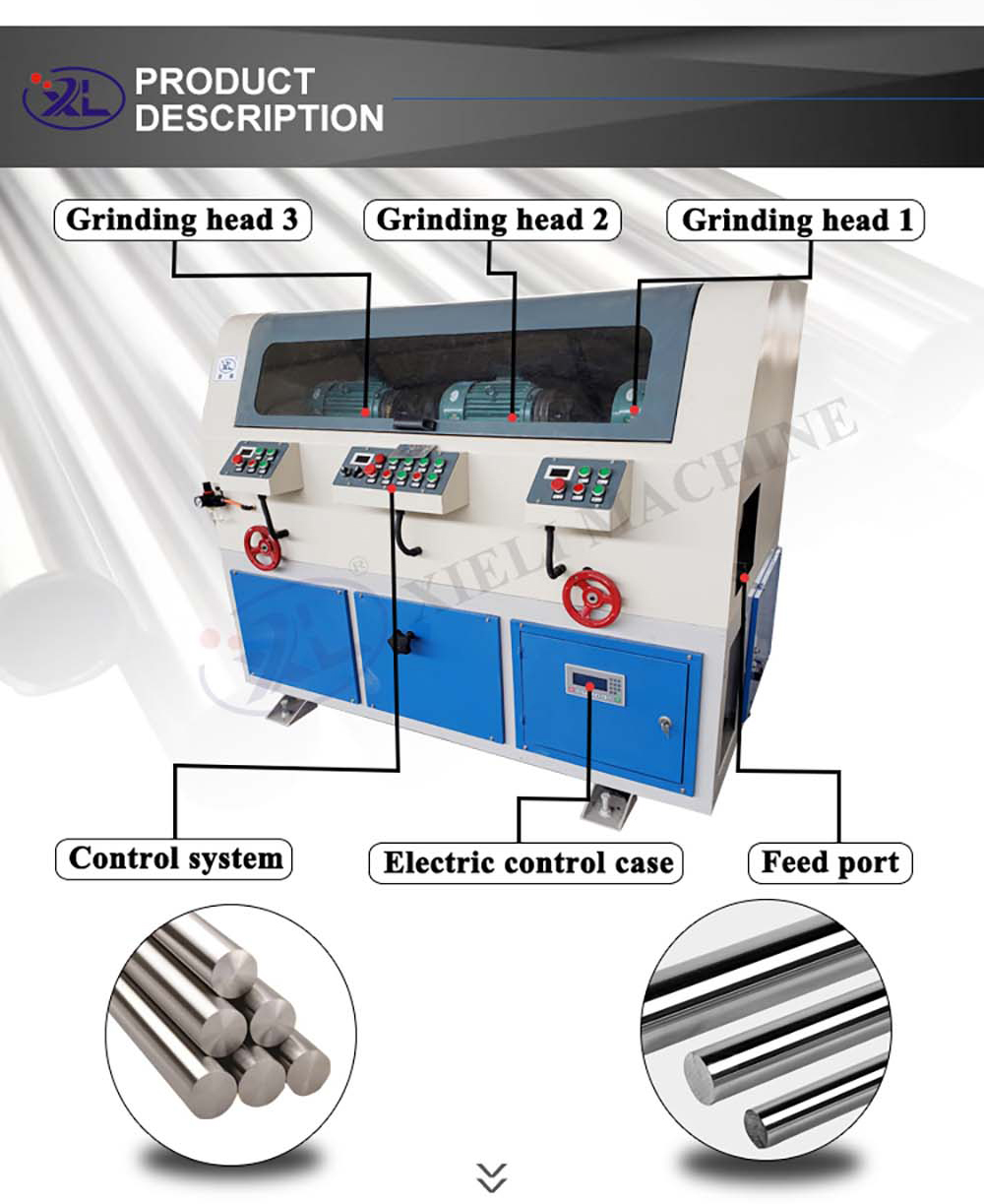
The type of coolant used can also significantly impact the efficiency and effectiveness of centerless grinding operations. Common types include water-based emulsions, synthetic coolants, and oil-based coolants. Each type has its advantages and disadvantages. Water-based emulsions are popular due to their cooling properties and cost-effectiveness, while synthetic coolants often provide better lubrication and reduced foaming. The choice of coolant should align with the specific requirements of the grinding process and the materials being processed.
In addition to temperature control and chip removal, coolants can also aid in the lubrication of the grinding wheel and workpiece interface. This lubrication reduces the wear on the grinding wheel, which translates to longer wheel life and lower replacement costs. Consistent lubrication can also enhance the grinding wheel's performance, allowing it to maintain its cutting efficiency over a longer period.
Safety is another consideration when discussing coolant in centerless grinding. Proper coolant management can minimize the risk of accidents caused by overheating or equipment malfunction. However, operators must also be cognizant of the health implications associated with certain coolants. Some fluids can be hazardous if inhaled or if they come into contact with skin, demanding rigorous safety protocols and personal protective equipment.
In conclusion, coolant plays an indispensable role in centerless grinding, impacting temperature control, chip removal, lubrication, and overall operational safety. Choosing the right coolant and employing it effectively can lead to improved performance, extended equipment lifespan, and superior product quality. As the manufacturing landscape continues to evolve, understanding the specifics of coolant in grinding operations is crucial for staying competitive and achieving excellence in production. Emphasizing the significance of coolant is not just an operational consideration but a pathway to ensuring quality and innovation in the manufacturing processes.